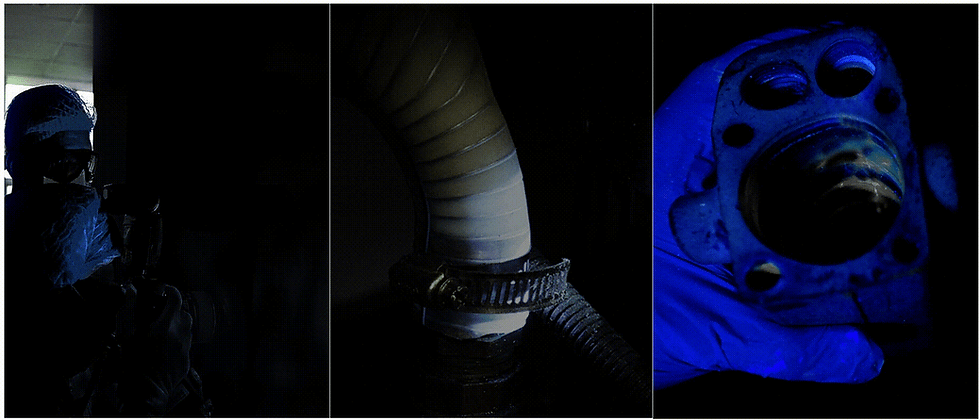
Nondestructive testing (NDT) is an essential process in various industries for evaluating the properties of materials, components, or systems without causing damage. One of the most effective methods of NDT involves the use of ultraviolet (UV) light. UV light, particularly in the UVA range (320-400 nm), is widely used for its ability to reveal defects that are otherwise invisible to the naked eye. Here, we will explore how UV light is used in nondestructive testing, the benefits it offers, and the steps involved in implementing this technique.
Table of contents
Understanding UV Light and Its Application in NDT
Ultraviolet light, especially UVA, is highly effective for nondestructive testing due to its ability to induce fluorescence in specific materials. When exposed to UV light, certain dyes and chemicals will fluoresce, making any defects or discontinuities in the material highly visible. This method is particularly useful in industries like aerospace, automotive, and manufacturing, where ensuring the integrity of materials and components is critical.
Benefits of Using UV Light in NDT
1. Enhanced Detection:
UV light can reveal fine cracks, porosities, and other defects that are not visible under normal lighting conditions. This enhanced detection capability ensures higher accuracy and reliability in inspections.
2. Non-Invasive:
As the name suggests, nondestructive testing does not harm or alter the material being inspected. This means that components can be tested in their final form, maintaining their usability and integrity.
3. Cost-Effective:
By detecting defects early, UV light NDT can prevent costly failures and repairs. It also reduces downtime as components do not need to be disassembled for inspection.
4. Versatility:
UV light NDT is applicable to a wide range of materials, including metals, ceramics, and composites. It is also useful in different stages of production, from raw material inspection to finished product testing.
Steps for Implementing UV Light NDT

1. Preparation of the Test Surface:
The surface of the material to be tested must be clean and free from contaminants. Any dirt, grease, or oil can interfere with the inspection process and lead to inaccurate results.
2. Application of Fluorescent Dye:
A fluorescent dye penetrant is applied to the surface of the material. This dye will seep into any cracks or defects present in the material.
3. Dwell Time:
Allow the dye to penetrate the defects for a specified period. The dwell time can vary depending on the material and the type of defects being sought.
4. Removal of Excess Dye:
After the dwell time, the excess dye on the surface is carefully removed, usually with a cleaner or a developer that does not affect the dye trapped in the defects.
5. Inspection Under UV Light:
The material is then exposed to UV light in a darkened environment. The dye trapped in defects will fluoresce, making any discontinuities visible to the inspector.
6. Documentation and Analysis:
Record the findings with photographs or written reports. Analyze the results to determine the severity and implications of the detected defects.
7. Post-Inspection Cleaning:
After the inspection, thoroughly clean the material to remove any residual dye and prepare it for further processing or use.
Best Practices for UV NDT
- Calibration:
Regular calibration of UV light equipment ensures consistent and accurate results. Calibration involves setting the light intensity and wavelength to the optimal levels for inspection.
- Safety Precautions:
UV light can be harmful to the eyes and skin. Inspectors should wear appropriate protective gear, including UV-blocking goggles and gloves.
- Environmental Conditions:
Conduct inspections in a controlled environment with minimal ambient light to enhance the visibility of fluorescent indications.
Conclusion
UV light NDT is a powerful tool for detecting defects and ensuring the quality and safety of materials and components. By following proper procedures and best practices, industries can leverage this technology to maintain high standards and prevent failures. Whether for routine inspections or critical evaluations, UV light nondestructive testing remains an invaluable method for quality assurance.
Comments